Future Fleets Report 2024
The report paints a picture of the equipment landscape and includes detailed profiles of mines that are employing these fleets
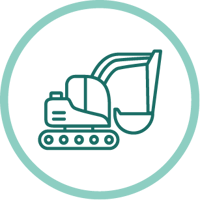
13.86%
Have operating cost below $10,000 per tonne for nickel concentrate
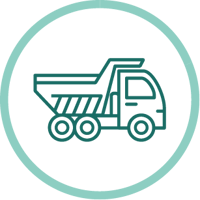
19%
The smallest mine in the table is Agnio Eagle Borden, with a production capacity of 280,000tpa
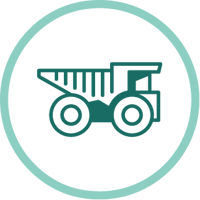
The largest mine in the report is Carajás, with a production capacity of 96.3Mtpa
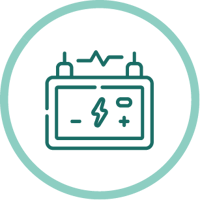
All of the mines with annual production capacities exceeding 30Mtpa are located in South America
The transition to electric drill rigs promises to not only reduce emissions but also enhance operational efficiency and productivity
Electric drill rigs lead the charge in 2023
A relentless drive by emerging automation and propulsion solutions into new segments of mining’s value chain ensured a dramatic year for the industry’s Future Fleets.
Long considered unfeasible due to engineering and economic constraints, electric drill rigs were one example of an emerging technology that made significant strides in 2023, largely driven by advances in charging solutions.
Major product launches from leading OEMs, like Epiroc’s SmartROC T35 E, showcased the feasibility and efficiency of electric drilling, paving the way for a cleaner and more sustainable surface mining industry.
The progress extended to underground operations, with Sandvik’s DL422iE battery-powered long-hole drill joining the company’s range of electric tunnelling jumbo and rock bolters, further demonstrating the potential of electric propulsion to boost safety and productivity underground.
Despite the breakthroughs, it remains to be seen if the OEMs can overcome concerns over the economic viability of electric drill rigs due to high battery and infrastructure costs, as well as the perceived inferiority of early electric drill rigs in terms of power output, reliability and overall performance.
However, the transition to electric drill rigs promises to not only reduce emissions but also enhance operational efficiency and productivity.
Bigger and better
Last year saw battery-electric mining trucks grow into sizes likely viewed as unimaginable by experts even a few years ago.
Fortescue took delivery of a 1.4MWh prototype battery that will be trialled in a 240t electric mining haul truck developed in partnership with Liebherr. The pioneering power system weighs 15t, measures 3.6m long, 1.6m wide and 2.4m high, and is made up of eight sub-packs, each with 36 modules – all individually cooled and each with its own batterymanagement system.
The largest battery-electric underground mining truck also started trials at Sunrise Dam in Australia in a three-way pilot between AngloGold Ashanti, Barminco and Sandvik. The 65t vehicle uses a lithiumiron phosphate (LiFePO4 or LFP) battery technology.
The electric driveline delivers 630 kW (858hp) of continuous power, allowing for high acceleration and shorter cycle times.
As well as producing zero diesel emissions underground and generating 80% less heat, the Sandvik TH665B is expected to be up to 25% faster on a 1:7 ramp than regular diesel trucks.
Australia's Mining Monthly Premium Subscribers can read the full report online.
If you'd like to subscribe or upgrade to a Premium Subscription, click here or contact the team at subscriptions@aspermont.com or on +44 (0) 208 187 2299.